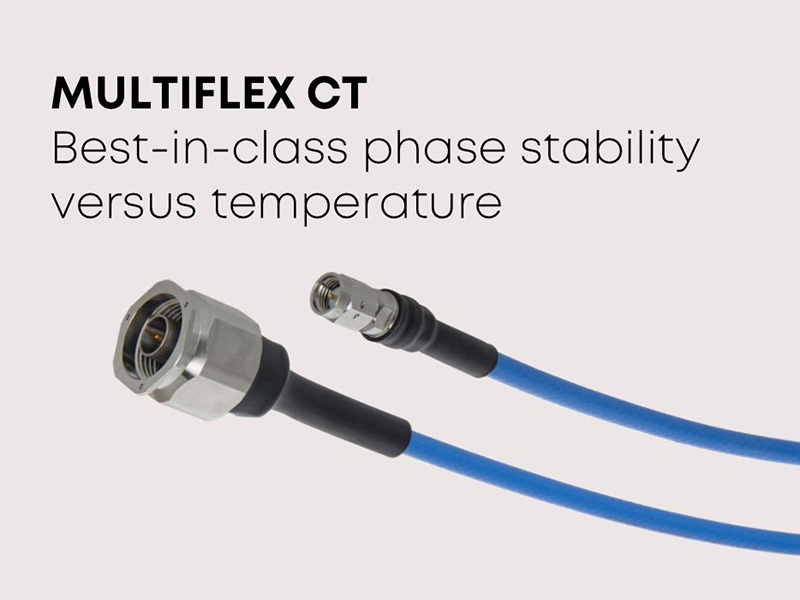
Today, PTFE (Polytetrafluoroethylene) dielectrics in coaxial assemblies (or Teflon as they are more commonly known) are widely considered as the “gold standard” for high performance RF applications in the aerospace [...]
yukaihl
Today, PTFE (Polytetrafluoroethylene) dielectrics in coaxial assemblies (or Teflon as they are more commonly known) are widely considered as the “gold standard” for high performance RF applications in the aerospace & defense market. This is due to PTFE’s superior combination of mechanical, electrical, and environmental performance characteristics among available dielectric materials.
The trade-off between performance and flexibility
However, PTFE as a dielectric material does have one significant shortcoming, which is its molecular transition at room temperature. This causes the dielectric constant (and therefore the signal’s phase) to abruptly shift in a predictable but inconvenient manner, when considering the signal integrity demands of high-resolution radars. This transition phase is known as the “PTFE knee”, which is shown in the image below, detailing phase vs. temperature plot.
There are several state-of-the-art manufacturing processes that exist to reduce the impact of this molecular activity by increasing the air density of the PTFE dielectric core. However, the PTFE knee cannot be completely eliminated.
Alternate dielectric materials, such as silicon dioxide, can be used in place of PTFE where the designer requires extreme phase stability over temperature and can afford to sacrifice the flexibility/pliability and insertion loss performance of the connection.
That being said, silicon dioxide cable assemblies are only available as pre-formed semi-rigid assemblies and have a bend radius that is at least twice as large as equivalent diameter PTFE cables. This means that the cost of ownership for them is very high, from procurement to integration. Historically, system designers have had to choose which of these tradeoffs the program can accommodate.
Uncompromised phase stability as well as mechanical and electrical performance
Design engineers will be glad to know that the days of sacrificing mechanical and electrical performance for phase stability are over.
HUBER+SUHNER’s proprietary foamed dielectric manufacturing technology significantly improves the phase stability performance of microwave cable assemblies over wide temperature profiles when compared to PTFE-based dielectrics, as demonstrated by the below data plot. This revolutionary dielectric technology minimizes insertion loss performance trade-offs, while mimicking the flexibility and pliability of its PTFE counterpart.
HUBER+SUHNER’s high-performance foamed fluorine polymer dielectrics are the cornerstone of our broad ‘Constant over Temperature’ (‘CT’) portfolio of flexible, hand-formable, and semi-rigid microwave cables. They provide phase-stable transmission up to V-band applications. The HUBER+SUHNER CT portfolio is available as qualified COTS cable assemblies and supports an extensive range of industry-qualified interfaces with highly competitive lead times.
FEATURES
- Excellent phase (300ppm typ.) and insertion loss stability over temperature
- Superior phase stability versus bending
- Outstanding return loss and shielding effectiveness performance
- Highly flexible for easy routing
- MIL qualified (MF_141 / 210 / 318 CT)
- Available with SS316L connectors
BENEFITS
- Increased system accuracy over wide temperature swings
- Stable system performance over multiple temperature cycles
- Improved loss performance vs. all other phase-stable cable options